TIMKEN needle roller and cage assemblies are a complement of needle rollers held in place by a cage. The mating shaft and housing are normally used as inner and outer raceways. The unitized design allows for easy handling and installation. Controlled-contour rollers reduce end stresses and permit operation under moderate misalignment. A variety of cage designs, styles and materials, as well as multiple roller paths and segmented constructions, meet broad application requirements.
- Sizes: 6 mm - 150 mm bore.
- Markets: Automotive and truck transmissions, agricultural and construction equipment, two-cycle engines, pumps and compressors.
- Features: Special coatings and platings; split and segmented designs for simplified mounting; engineered polymer cages.
- Benefits: High load capacity and high limiting speed within the smallest envelope.
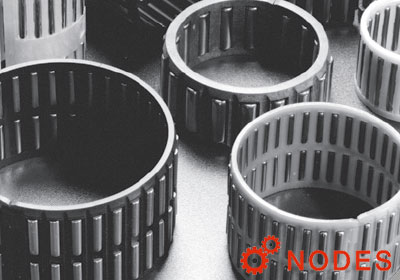
TIMKEN needle roller and cage radial assemblies have a steel cage that provides both inward and outward retention for the needle rollers. The designs provide maximum cage strength consistent with the inherent high load ratings of TIMKEN needle roller bearings. Accurate guidance of the needle rollers by the cage bars allows for operation at high speeds. Needle roller and cage assemblies have either one or two rows of needle rollers.
Also listed are metric series needle roller and cage assemblies using molded, one piece glass reinforced engineered polymer cages (suffix TN). These operate well at temperatures up to 120° C over extended periods. However, care should be exercised when these assemblies are lubricated with oils containing additives as service life may be reduced if the operating temperature exceeds 100° C. At such high temperatures oil can deteriorate with time and it is suggested that oil change intervals are observed.